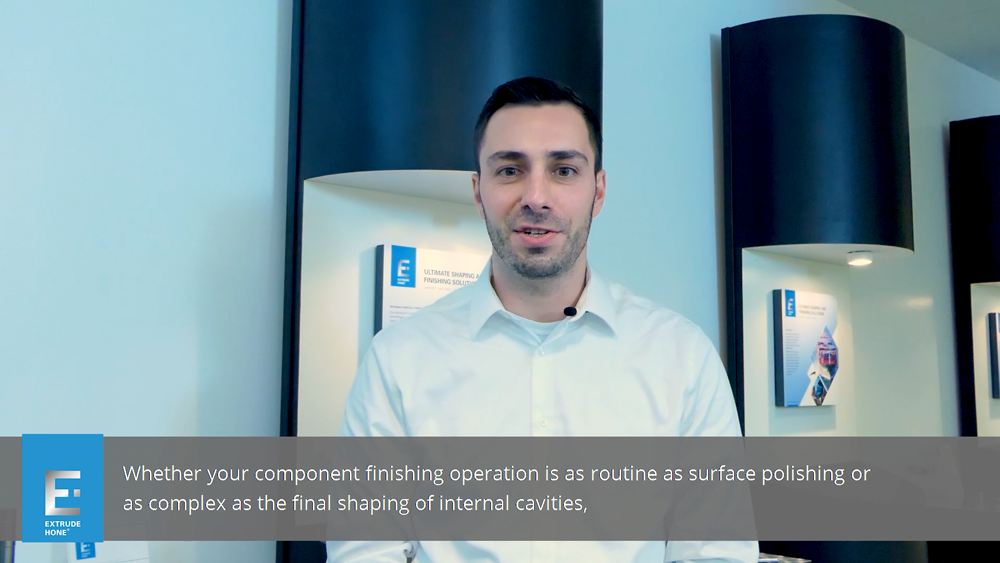
Renishaw and Extrude Hone address finishing on 3d printed titanium parts
Extrude Hone processes ensure complete removal of partially-sintered material on internal surfaces of a complex titanium manifold.Extrude Hone has been a leader in finishing since the 1960’s, working closely with the aerospace, automotive, medical and energy generation supply chains to improve mechanical properties of parts for increased component life and to improve fluid dynamic properties of parts for improved fuel efficiency, all whilst offering productivity gains in manufacturing. Recognized as the industry’s ‘problem-solver’, Extrude Hone has more recently been approached by companies facing challenges in internal and external surface finishing for Additively Manufactured components.
For most, Renishaw need no introduction. Recognized as one of the leading companies in the additive manufacturing sphere, not only for their machinery but also for their application engineering and ability to prescribe complete additive solutions to customers, it is no surprise that some of the world’s leading OEMs across various industries place their trust in Renishaw. For more information about Renishaw’s additive solutions, see: http://www.renishaw.com/en/additive-manufacturing-systems–15239
In order to provide a complete solution, finishing must be considered but can be a hard nut to crack due to the relatively rough surfaces and complex geometries produced by Additive Manufacturing techniques.
Renishaw tasked Extrude Hone with the complete removal of partially-sintered and unsintered material on the internal surfaces of a titanium demonstrator part (designed by MOOG) representative of an aerospace manifold which was built using Renishaw’s industry-leading quad laser technology. Being manufactured additively, the manifold had organic features including convoluted passages with no line-of-sight and diameter changes along bores making this application a very tall order for most finishing processes.
Using a combination of its Abrasive Flow (AFM) and COOLPULSE , Extrude Hone was able to remove all partially sintered material and improve the roughness of all internal surfaces, COOLPULSE being used for in the main bores with steps in diameter and AFM being used for the convoluted passages.
Here are the results:
Primary Objective: Remove all partially sintered and unsintered material
COOLPULSE:
Control Surface – SEM x200 Magnification
COOLPULSE Surface – SEM x200 Magnification
Abrasive Flow Machining (AFM):
Control Surface – SEM x200 Magnification
AFM Surface – SEM x200 Magnification
Secondary objective: Improve surface roughness
Results:
Control Surface
After EH processes
Statement from Renishaw’s Alex Freeman (Senior Development Engineer – Special Projects):
“We approached Extrude Hone due to their reputation in the field of internal surface finishing. After processing the demonstrator with Abrasive Flow and COOLPULSE, we were unable to detect any partially sintered material on the internal surfaces of the manifold. We also noted improvements in the surface roughness, of particular interest were the small internal non-line-of-sight channels. We consider the results of the trial to be very promising and will be suggesting Extrude Hone’s AFM and COOLPULSE processes to customers with similar design requirements to this demonstrator. The internal surfaces are the most advanced we’ve seen to date.”
Extrude Hone finishing solutions are suitable for aluminum, stainless steel, Inconel, and titanium and can address a broad range of geometries meaning that most 3D-printed components can be finished by an Extrude Hone technology or combination of technologies.
Demonstrating its commitment to additive technology, Extrude Hone recently set up a brand-new business unit called ‘Extrude Hone Additive’ and is aiming to establish itself as the ‘go-to’ partner for additive finishing as the industry grows and matures.
For more information on Extrude Hone’s additive solutions: