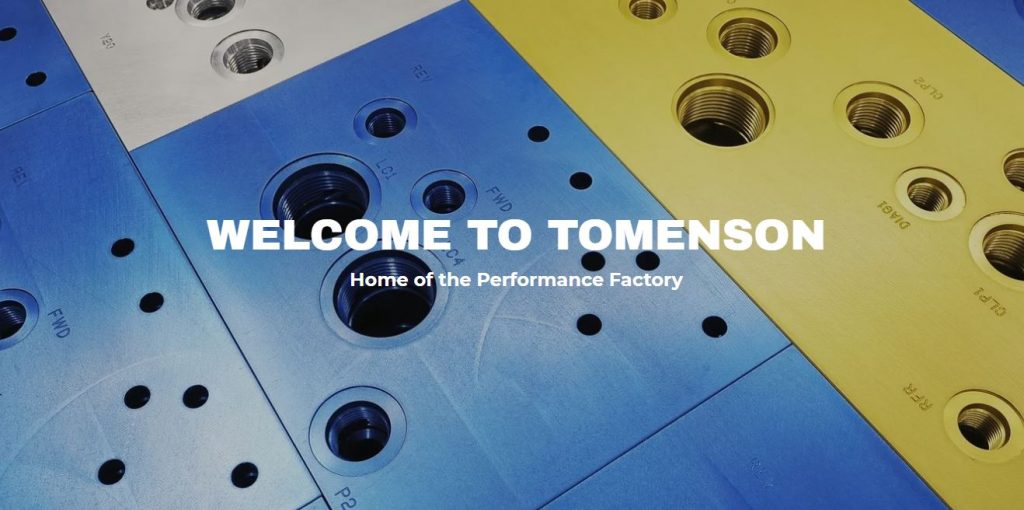
TOMENSON IMPLEMENTS EXTRUDE HONE THERMAL DEBURRING
The importance of an adequately deburred hydraulic manifold can be understated.
With most manifolds with hundreds, even thousands of dimensions, deburring is often a second thought to customers and manufacturers.
However, when it comes to hydraulic manifolds, proper deburring is critical. Hydraulic failures most often occur due to contamination found in the hydraulic system. Burrs and loose contaminants are often the cause, both of which can be found within a hydraulic manifold and are challenging to detect and remove.
Tomenson’ s deburring before September of 2018 was 100% manual deburring using scrapers, abrasives, drills, and taps. To ensure proper deburring of our manifolds, 30-35 seasoned employees with a combined 210 years of experience and 100% visual inspection was the reliance Tomenson had on burr-free manifolds. Customers have historically applauded Tomenson’ s deburring for both quality and consistency. However, it has always been clear that the task is difficult, time-consuming, and challenging to train.
In 2018, Tomenson experienced a breakout year with record sales, and over 400,000 hydraulic manifolds shipped. It quickly became evident that the bottleneck was often the deburring department. With the difficulty of training new employees, the process was tough to scale. Tomenson then looked at technology and automation to solve this problem. At this time, a partnership with Extrude Hone formed.
With an immediate need for scalability, Tomenson first began using Extrude Hone’s production shop in Huntly, IL, which provides thermal deburring services for ductile, steel, and aluminum parts. Spending a year with this service, Tomenson reduced every manifold’s deburring time on average by at least 50%, with some manifolds experiencing an 80% reduction in manual deburring time.
“Thermal deburring reduced the manual deburring time of a hydraulic manifold from 90 minutes/part to 16 minutes/part.” – Zach Roake, General Manager.
Throughout 2018-2019, Tomenson learned the benefits and limitations of the thermal deburring process. After trialing the process for a year, it was clear that thermal deburring was an excellent solution to scale with production, reduce defects, and reduce labor. Tomenson then decided to purchase Extrude Hone’s largest standard thermal deburring machine, the five-station TEM T450.
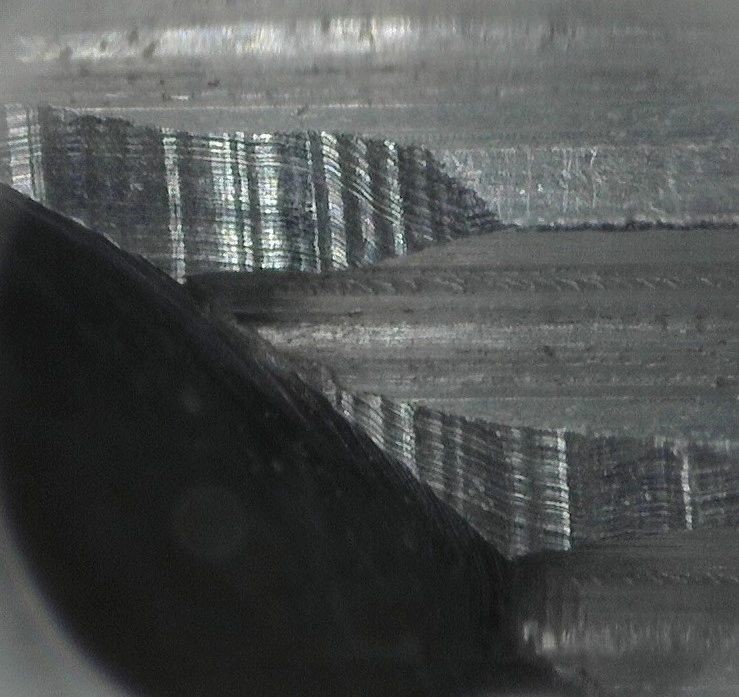

Since implementing thermal deburring, Tomenson has reduced its deburring staff from 35 to 10 employees while maintaining the same, if not better quality its customers expect. Also, overall part cleanliness has been easier to maintain.
“Extrude Hone has played an important part in terms of automating a heavily manual process. Throughout the learning, implementation, and maintenance of the new machine, they have been readily available for questions, training, and support.” – Zach Roake, General Manager.
Thermal deburring with Extrude Hone has reduced lead times, reduced labor, and improved overall part quality.
Read the original document on Tomenson’ s website.
Want to learn more about TEM- Thermal Deburring, we invite you to visit the T Series product page, with all data in a single place.