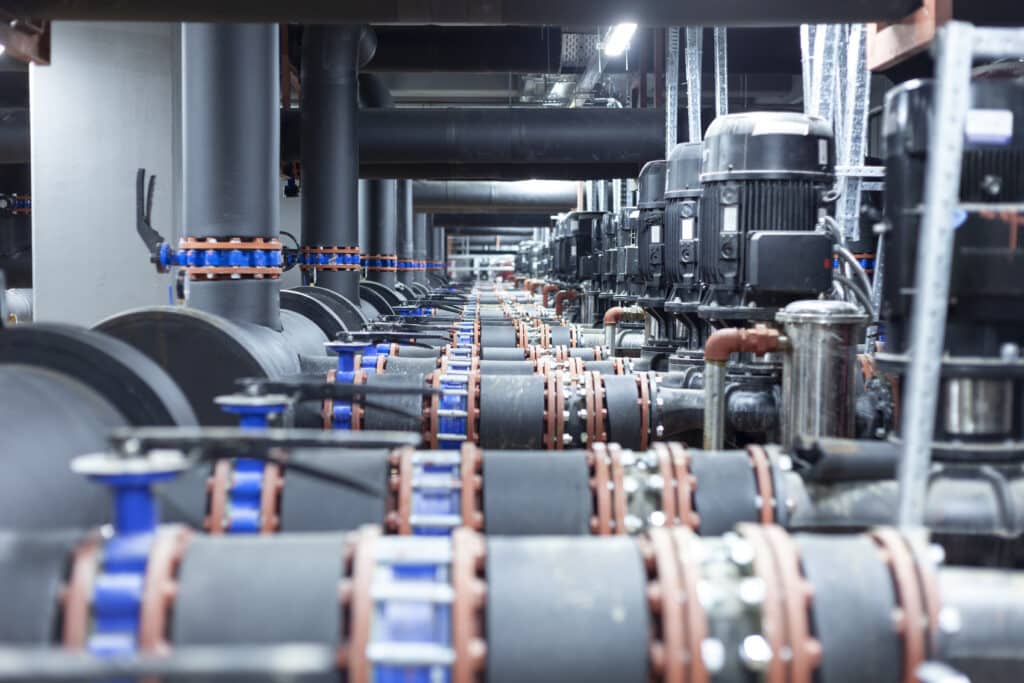
SMALL MANIFOLDS BURRS LEAD TO BIG PROBLEMS
Small burrs may seem insignificant, but they can lead to significant problems, particularly in critical components like “mission-critical manifolds” used in high-productivity and no-downtime environments.
Burrs can jeopardize the fluid power system’s integrity.
Burrs can compromise the design integrity, cause safety hazards, and result in a product malfunction, leading to additional costs, re-manufacturing, warranty claims, and damage to a company’s reputation.
Contamination of fluid system :
Burrs can break off and become loose particles within the fluid system. These particles can act as contaminants, circulating within the system and potentially damaging sensitive components such as valves, pumps, or actuators.
Contamination can lead to system failures, decreased performance, and increased maintenance requirements.
Burrs can interfere with operating valves, actuators, or other components within the manifold. They can prevent components from seating properly, hinder the movement of moving parts, or cause jamming.
This can result in system malfunctions, loss of control, and potential safety hazards.
Flow restriction
Burrs can obstruct fluid flow within the manifold, reducing the efficiency and performance of hydraulic or pneumatic systems.
This restriction can result in decreased system responsiveness, slower operation, and inefficiencies in fluid distribution. It disrupts the smooth flow of fluid within the manifold, leading to turbulence, pressure drops, or inefficient fluid distribution.
This can reduce system efficiency, increase energy consumption, and decrease overall performance.
System leakage
Burrs can create irregularities in sealing surfaces, causing leaks in the system. These leaks can lead to fluid loss, decreased system pressure, and potential contamination of surrounding components or environments.
In critical applications, such as aerospace or medical devices, leakage can have severe consequences.
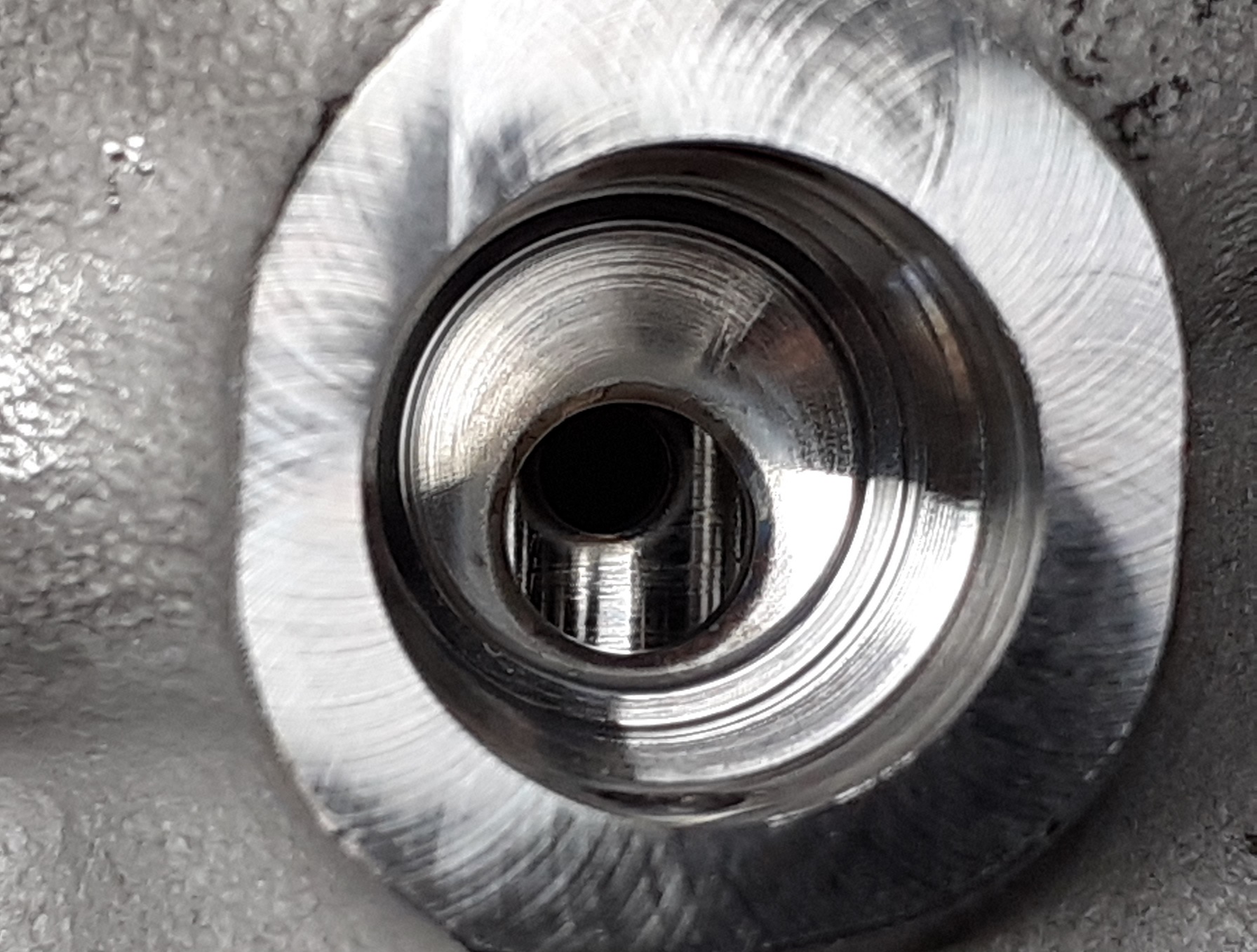
Component wear
Burrs can cause excessive wear on mating components or seals within the manifold, creating frictional forces that accelerate wear and prematurely fail components.
This can increase maintenance costs, downtime, and decreased system reliability.
In demanding applications like fluid power systems, even minor leakage or breakdowns can have devastating consequences.
As such, it is crucial to remove or secure burrs to prevent them from detaching and causing potential issues.
Thermal deburring for optimum fluid power system finishing.
TEM, known for its efficiency and productivity, is widely applied in the fluid power industry to deburr components such as valve bodies, manifolds, spools, pump and hydraulic motor elements, cylinder components, hydraulic fittings, and threads.
How does the thermal deburring process work?
The process of thermal deburring involves igniting a pressurized mixture of combustible gas and oxygen within a sealed chamber, generating intense heat energy that vaporizes burrs and flashes without affecting the workpiece’s metallurgical properties.
TEM is known for its speed and efficiency, with cycle times typically less than a minute per component.
TEM works by subjecting the components to super-heated gas, reaching temperatures of up to 3,300°C (6,000°F) in milliseconds, effectively vaporizing burrs and particles without impacting the component. More about TEM for manifolds in our whitepaper.
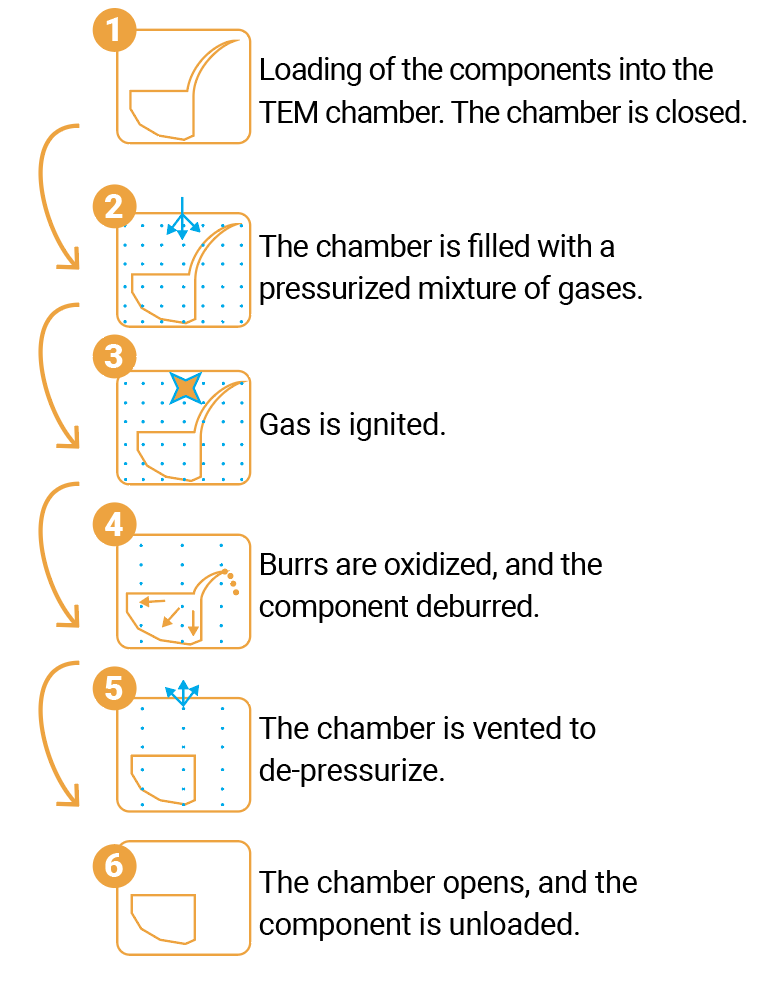
Superior advantages of thermal deburring
Post-treatment involves cleaning the oxide layer left on the surface after deburring. Chemical cleaning solutions remove the oxide layer, ensuring the components are contaminant-free.
Thermal deburring (TEM) emerges as a solution to this challenge, offering a method to effectively eliminate burrs and particles from various materials such as cast iron, steel, stainless steel, zinc, aluminum, brass, and some thermoplastics.
The benefits of TEM include speed, integrity, and low cost per part. Compared to manual deburring, TEM offers reliability and consistency, eliminating the need for further inspection and skilled labor.
Additionally, TEM is a cost-effective solution, providing superior deburring quality at a fraction of the cost of traditional methods.
Deburring methods comparison
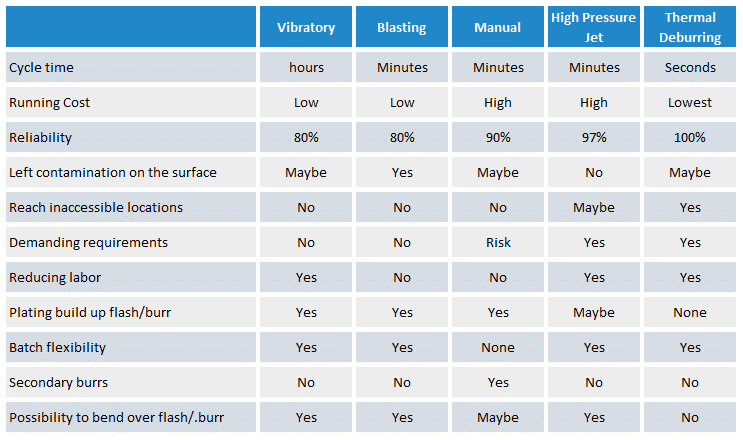
How do you access thermal deburring technology?
Thermal deburring machines
Extrude Hone’s TEM machines, like the T series, provide fast and reliable solutions for removing all internal and external burrs simultaneously in a single operation.
Moreover, Extrude Hone provides tooling and accessories for thermal deburring equipment.
Contract shops for thermal deburring services
Our network of contract shops is aimed at those with smaller volume requirements who don’t need or want to buy a machine.
Leveraging Extrude Hone’s contract capabilities provides customers access to experienced professionals and ensures quick turnaround times without compromising quality.
Extrude Hone’s overarching goal is to enhance efficiency and produce flawless parts.