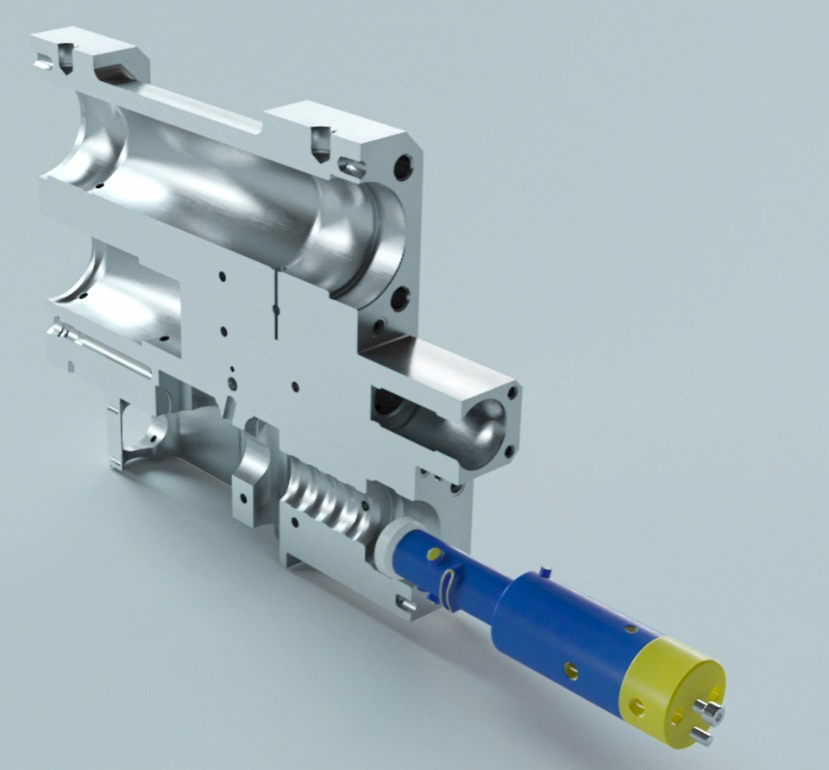
Mr. Siddhartha Sirdeshpande’s inspiring electrochemical machining (ECM) journey.
Mr. Siddhartha Sirdeshpande, a seasoned operation leader, shared insights from his extensive career in various industries, focusing on his experiences with Electrochemical Machining (ECM) technology.
With a background in precision machining in the aerospace and automotive sectors, Sirdeshpande discussed his journey from automotive to aerospace, highlighting the pivotal role of ECM technology.
Look out for the whole interview here, made by Bruno Boutantin, Market & Business Development Director for the Extrude Hone Group.
Mr. Siddhartha Sirdeshpande’s background and experience with ECM
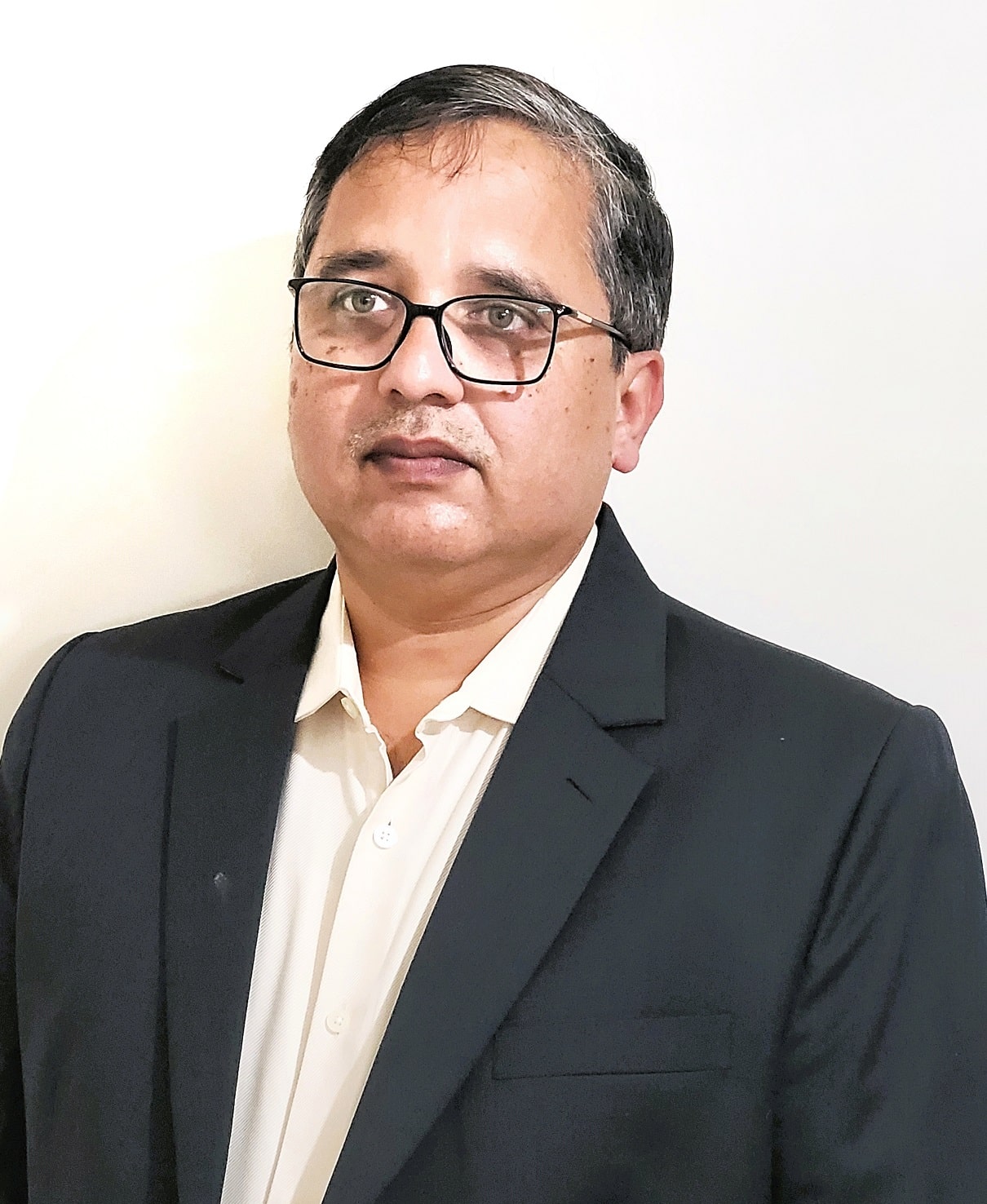
Mr Siddhartha Sirdeshpande :
- Experience: Nearly 28 years in industries including hydraulics, steel manufacturing, heavy fabrication, and wire and cable extrusions.
- Roles: Vice President Adani Defence and Aerospace, Chief Operating Officer at Maini Precision Products, Thermocables, RSB Transmissions; General Manager at UT Limited.
- Focus: Precision parts manufacturing according to customer specifications, particularly aerospace and automotive.
About ECM Technology in Automotive
Mr Siddhartha Sirdeshpande’s ECM challenges began with Gasoline Direct Injection (GDI) pumps in the automotive industry.
Manufacturing complex parts with tight tolerances and ensuring safety by eliminating burrs and sharp edges in high-pressure environments was a real challenge, so the adoption of ECM technology to achieve precision and consistency was a good choice.
But GDI Pumps (Stainless steel forged body with complex machining requirements, critical to handle 400-600 bar fuel pressure without burrs) enabled precise deburring and consistent quality, reducing safety risks.
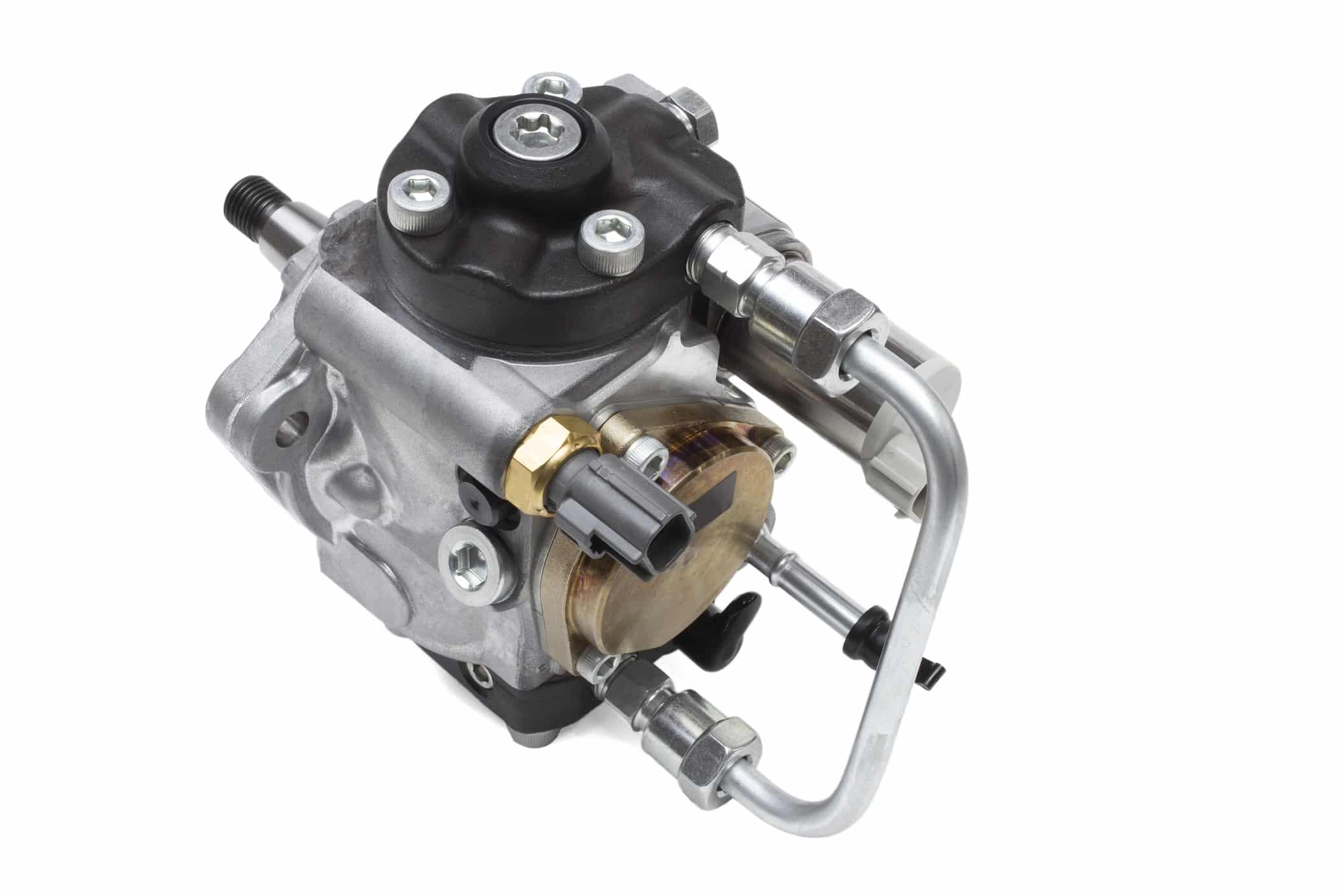
“So, initially, when you had the lower version of this thing, the 100-bar capacity version, I was using a lot of Indian-made machines on it. One of the issues I found is that stainless steel with chromium forms chromates, which then becomes hazardous.
So, I was also looking forward to when we developed the sixth generation. Uh, that next-generation GDI with 600 bar pressure for Mazda, basically through Marelli, but the end customer was Mazda Japan. As the single manufacturer of that thing, maintaining a specific radius at the intersections was a critical requirement.
So, the intersections are not approachable from the outside, and we need to maintain a specific radius. So that was a critical thing. So, then, I came across, okay, let’s have a solution from Extrude Hone. I got one machine for this, and it served the purpose. Then, subsequently, I developed all the other GDI on the same Extrude Hone machine.
So, basically, that has given the technical solution for getting the parts right the first time and consistently. So, initially, I faced some issues related to procuring the tools and maintaining the inventory.
But then, in that area, the Extrude Hone India team supported me, and then they told us, OK, based on your requirement, we can carry some of the tool inventory so that you don’t need to carry that thing.
The lead time can be reduced or something like that. Then I could run this thing. So, I was still depending on Extrude Hone for the tooling part of these machines.
But then, after that, when I found a similar application in aerospace, for which I could do ECM, the aerospace industry was not using Extrude Hone.”
ECM aerospace push
Mr Sirdeshpande pushed for ECM adoption in aerospace, highlighting efficiency and quality improvements.
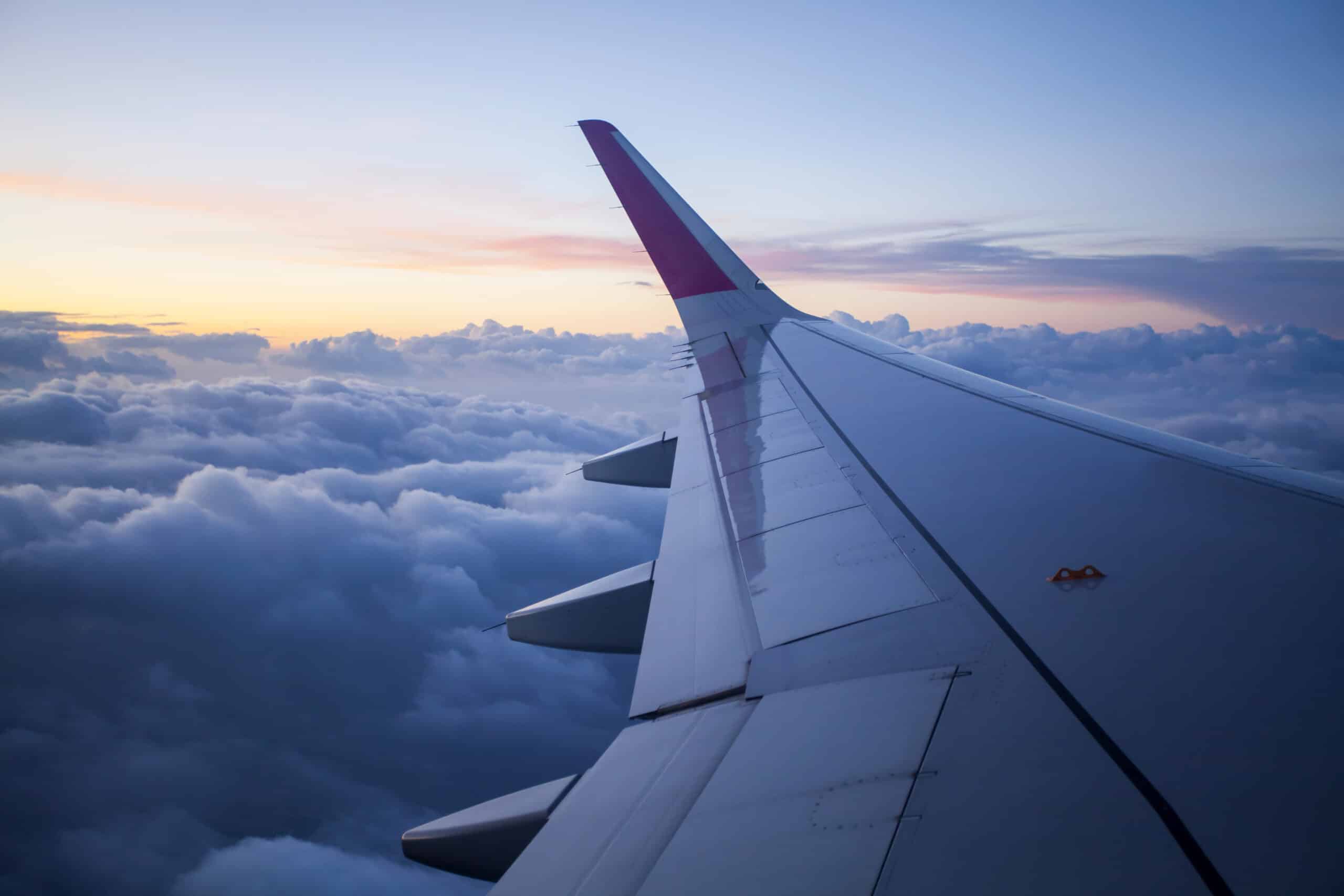
Case Study: Aerospace
Project: developed ECM processes for aluminum manifolds in aerospace.
ECM benefits :
- Results: a significant reduction in deburring time (from 4.5 hours to 2.5 minutes per component), improved quality.
- Consistency: stressed ECM’s advantage in maintaining consistent quality
- Recommendation: suggested pushing ECM from the OEM side for easier adoption by component manufacturers.
“So once that development is completed, Safran could approve. Maybe for the aerospace industry component manufacturing, this would be the first process of going out of manual deburring and then introducing the ECM deburring process. So, there are advantages to this thing.
You can save a lot of manpower and time on this thing because presently, on the aluminum manifold on aerospace, I was spending almost four and a half hours per component for debris, that too with a skilled mentor. But if it comes through extrude hone, this activity will be a maximum of two and a half minutes that we have done that thing.
That will be a massive change. Apart from that, it will completely reskill the operator activity. This will help because it will be more process and tool-controlled. That is the area where I thought Extrude Hone had the right solution to this. And this is the way forward.”
Dassault reference in using ECM for aerospace components
Bruno Boutantin :
“ Now they (Dassault Aviation) have this fantastic machine, a three-station / three-tooling machine that processes quite complex parts with more than 300+ locations to be processed. And they deburr, radius, and polish, all simultaneously”.
“When you do these things manually, you are never sure of the quality, especially when looking at the tolerances. In addition, you will need 100 percent control if you do this by hand, if you use a machine, you can rely on the machine.”
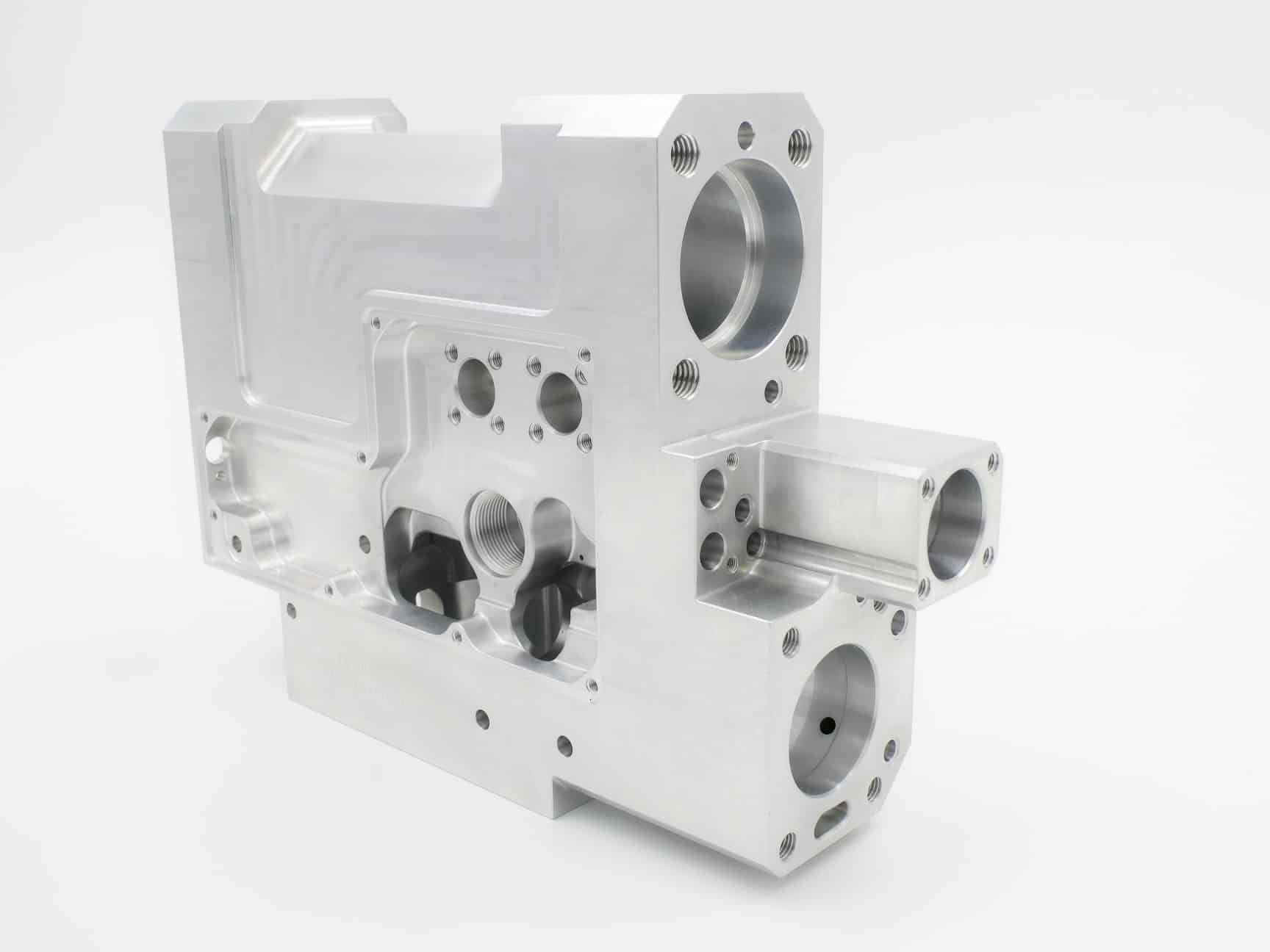
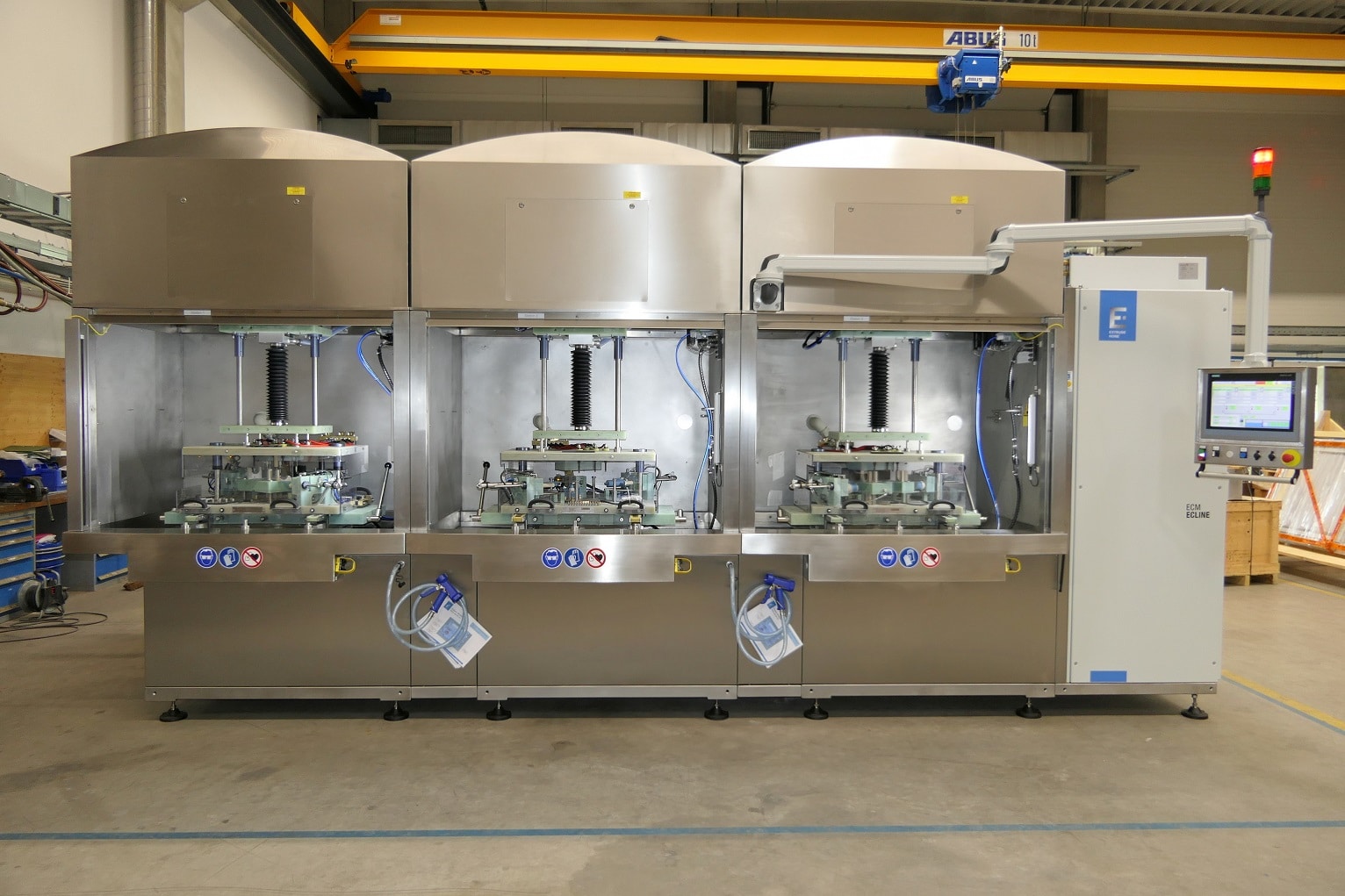
Mr Siddhartha Sirdeshpande’s experience with Extrude Hone
In the Indian market, there are cheaper ECM alternatives. So why choose Extrude Hone’s machines?
Extrude Hone’s ECM machine’s performance
“In India, a lot of other ECM machines are available, and those are, I would say, about 20 percent of the cost of your machines, right?
So, and it is not that every, and the quality of those machines, if I say, okay, maybe the safety side, it has more compromise in some areas. Still, the quality, wherever you have specific tolerances on the deburring, then it becomes more complicated for the other manufacturers to pitch in”.
But, in most cases, eight out of 10 will call only for the simple deburring. It will not ask for any specific dimension on the deburring. It should be a clean, clean hole where there should not be any detachable work. So, to that extent, the other machines can also meet that requirement in terms of quality.
Now comes only the two cases out of 10 where the specific complex requirements are there that I need a specific radius to be formed.
In that case, I could not find a solution at present, but there are many people, in many ways I introduced this machine to a great OEM I worked for, and there are two, or three other manufacturers who came and discussed with me that we also have the machines and there are, people are coming up every, every year.
So, when I started this, it was only two. Now I think we have five or six manufacturers in India who manufacture the ECM machines. So, I’m not saying technically how it is compared to this thing. I’m seeing from the user’s perspective, that there is a chance that if I’m not seeing a complex drawing requirement, then people may tend to go to the others.
So that is one area. So, you need to hard pitch from the OEM side, particularly in aerospace, where the requirements will be complex. So, it will make the Extrude Hone’s ability to deal with complex requirements the solution.”
Extrude Hone’s Indian team support
“(…) Mr. Debnath and his team are also coming to their customers, so for any technical assistance, their team and your team can work together and do it.
Of course, if you are in Bangalore, it’s easy. It’s also easy logistically. So, I treat Extrude Hone India as one of my extended arms. So, then it is, it’s not an issue for me regarding getting training.
We have resolved the specific technical issue. Later, I had to develop four variants of gasoline direct injection pumps, and we developed the fixture for the same machines. So, fixtures also come from the India team—your Indian team. So, I get good support from them. It’s not an issue at all. I have a good relationship with Debnath.”
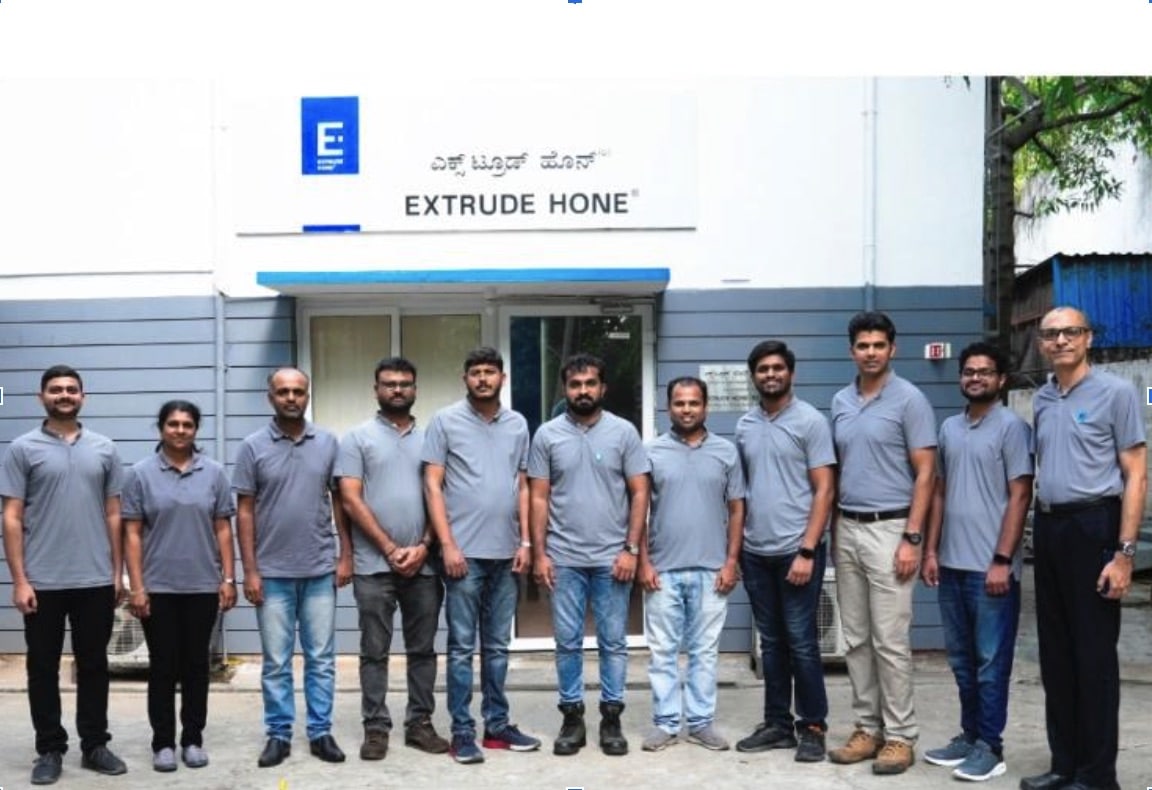
We thank Mr. Siddhartha Sirdeshpande for sharing his strong, seasoned senior industry expertise with this highlight on ECM technology adoption. At Extrude Hone, we look forward to continuing to support Indian industry leaders.
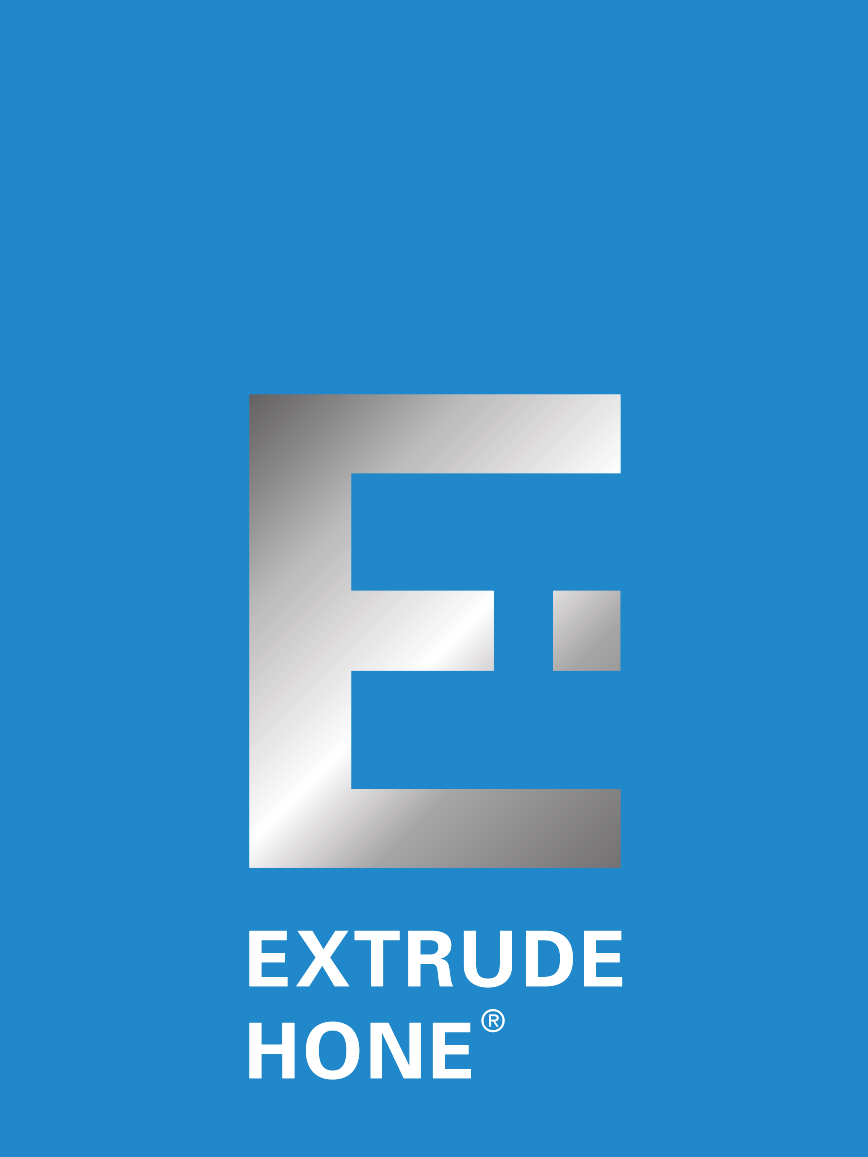
Interviewer :
Bruno Boutantin
Marketing Director Extrude Hone Group
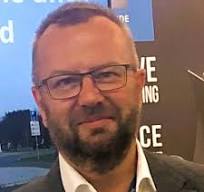